Basic
Design of the Shredding Mechanism:
Royer uses the same cleated high speed shredding belt design on all
models to churn, pulverize, and aerate the material. The width and
length of the shredding belt increases with each larger model. The
cleats are approximately 5/8 inch high, hardened metal strips riveted
closely together crossways on a continuous conveyor belt. Above and
perpendicular to this belt at the discharge end are metal plates or
blades. These blades run continuously across the belt to provide a
striking surface for any oversized material. Royer calls this mechanism
the "sweep". The adjustable gap between the blades and the cleats
provides an opening for shredded material to exit. Oversized materials
[e.g., stones] tumble backwards, since the shredding belt is at a steep
angle, fall out a chute onto a "trash" conveyor, and are piled along
side of the machine. Please see "Patented Four-Step Processing Action"
for more details.
Patented Four-Step Processing Action:
After material is loaded into the hopper
of a Royer, a feed conveyor carries it up to the shredding chamber [1]
where it cascades onto the shredding belt [2]. There, the material is
thoroughly churned while rows of steel shredding cleats rake and aerate
the load. Fully processed material discharges under an adjustable sweep
[3]. Oversize lumps fall back for further processing. Non-shreddable
materials and debris are separated automatically and discharged through
a trash chute [4]. The result is a light, fully aerated product that’s
clean, uniform in particle size, and free of unwanted materials.
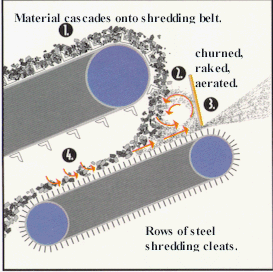
|